
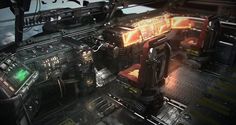
For the flight control system to keep the whole system stable, the ability to initiate a maneuver easily needed to be moderated. Air Force tests did not support this expectation. This perception has held up in the years following the end of flight tests. The high pitch instability of the airframe led to wide predictions of extreme maneuverability. It was estimated that a total failure of the system was as unlikely as a mechanical failure in an airplane with a conventional arrangement. Each of the three would "vote" on their measurements, so that if any one was malfunctioning it could be detected. The flight control system was made up of three redundant digital computers backed up by three redundant analog computers any of the three could fly it on its own, but the redundancy allowed them to check for errors. Stability was provided by the computerized flight control system making 40 corrections per second. The configuration, combined with a center of gravity well aft of the aerodynamic center, made the craft inherently unstable. The canards and wings result in reduced trim drag and reduced wave drag, while using the strakes for trim in situations where the center of gravity is off provides less trim drag than relying on the canard to compensate. The X-29 is described as a three surface aircraft, with canards, forward-swept wings, and aft strake control surfaces, using three-surface longitudinal control.
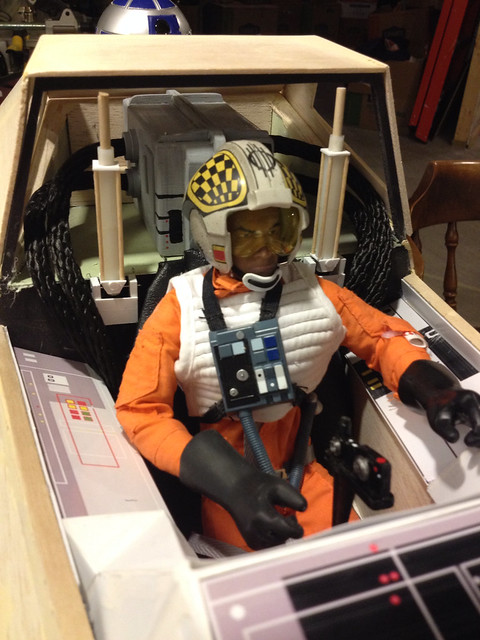
X-29 cockpit Three-surface design and inherent instability The Grumman internal designation for the X-29 was "Grumman Model 712" or "G-712". The wings of the X-29, made partially of graphite epoxy, were swept forward at more than 33 degrees forward-swept wings were first trialed 40 years earlier on the experimental Junkers Ju 287 and OKB-1 EF 131. The technological advancement that made the X-29 a plausible design was the use of carbon-fiber composites. The control surface actuators and main landing gear were from the F-16. The X-29 design made use of the forward fuselage and nose landing gear from two existing F-5A Freedom Fighter airframes (63-8372 became 82-0003 and 65-10573 became 82-0049). Two X-29As were built by Grumman after the proposal had been chosen over a competing one involving a General Dynamics F-16 Fighting Falcon. The aircraft first flew in 1984, and two X-29s were flight tested through 1991. Composite materials were used to control the aeroelastic divergent twisting experienced by forward-swept wings, and to reduce weight. The aerodynamic instability of the X-29's airframe required the use of computerized fly-by-wire control. The X-29 was developed by Grumman, and the two built were flown by NASA and the United States Air Force.

The Grumman X-29 was an American experimental aircraft that tested a forward-swept wing, canard control surfaces, and other novel aircraft technologies.
